What is Digital Manufacturing FJVPS
Digital Manufacturing FJVPS is a software package that covers the entire process of production preparation, using 3D model data of products created in CAD tools for product reviews, process reviews when assembling products, production line layout reviews, and creating documents used in manufacturing, in order to support the smooth start-up of mass production.
Production preparation for mass production is often close to be late for the delivery deadline because of a delay of the previous process. Digital Manufacturing FJVPS enables the manufacturing division to review a product in an early stage of the design process, so that the division is able to communicate earlier to the design division about possible failures during assembly or improvement requirements. This efficient communication flow promotes product development for which the factory circumstance or manufacturability is sufficiently considered.
FJVPS enables you to easily verify the complex mechanism of a product during the design process. Digital Manufacturing FJVPS ensures simple mechanism setting using a wizard form and provides comfortable manipulation even for the model with large data by using its own lightweight system.
Digital Manufacturing
FJVPS Key Benefits
Digital Manufacturing FJVPS realizes, improvement of quality and production time of the early period of mass production as well as early improvement with design quality. The simple operation that even a CAD inexperienced person is usable. |
|
|
|
QUALITY IMPROVEMENT |
|
• 50-80% of the design error was detected on a virtual prototype beforehand.
• The remaining defect item concerning assembly vanished before it approved.
• The drawing change rate after approval became 1/6.
• Defective assembly was able to be reduced to 1/5 in 1.5 years.
• The assembly trouble reduction 80% that was the initial goal was achieved in four years.
|
|
|
|
|
|
|
|
PRODUCTIVITY ENHANCEMENT AND COST REDUCTION |
|
• The start-up period of the prototype was able to be adjusted to 1/15.
• The development period was shortened to six months, and the development cost was reduced to 1/2.
• FJVPS harness option was used, and the design period was able to be moved up for one month. |
|
|
|
|
|
|
|
|
SHORTENING AT LEAD TIME AND PERIOD |
|
• The man-hour of making the work procedure manual has been reduced by 30-40%.
• Communication between design and other business segment have been improved.
• Suggestions for improvement (ex. Mechanism operation, assembly, and check of serviceability) became possible without a real machine.
• The metal mold correction cost was reduced by half by the front-loading by FJVPS. |
|
|
|
|
FJVPS Case Study
|
|
Murata Machinery Ltd.
(Manufacturing and Sales of Logistics Systems, FA Systems, Clean FA, Machining Tools, Metal Sheet Processing Machines, Textile Machinery, Information Equipment, etc.) |
|
Concurrent Engineering: Delivering Better Producst, Faster |
|
Lear more |
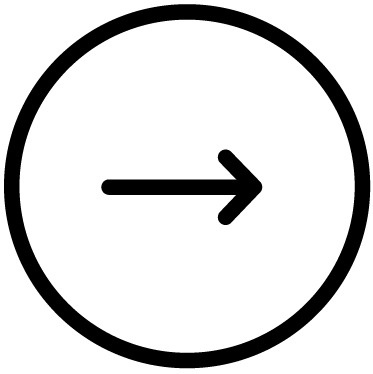 |
|
|
|
|
|
Mitsubishi Electric Engineering Co., Ltd.
(Development & design Electronic equipment) |
|
Transformation of Escalator Development Process through the Utilization of 3D Data with FJVPS Implementation |
|
Lear more |
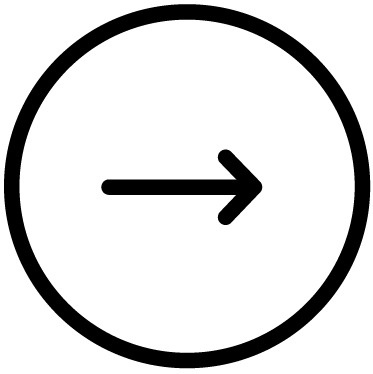 |
|
|
|
|
|
PHC Holdings Co., Ltd.
(Development, manufacture, and sales of various healthcare) |
|
Demand-driven and Proposal-driven, 2 types of Deployment |
|
Lear more |
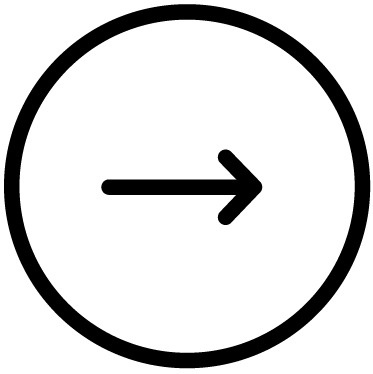 |
|
|
|
|
|
Tokai Rika Co., Ltd.
(Various automotive switches, key locks, seat belts, shift levers, electronics application products, steering wheels, connectors, mirrors, plastic wheel covers, ornaments) |
|
Revolutionizing Production Preparation with 3D Utilization |
|
Lear more |
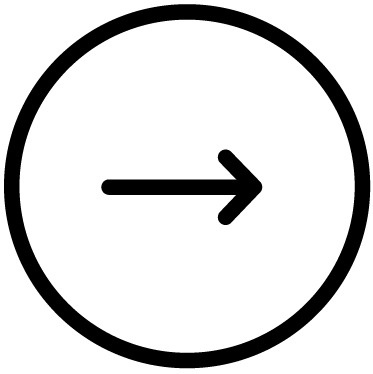 |
|
|
|
|
|
Shimadzu Corporation (Analytical & measuring instruments) |
|
|
|
|
THE START OF PRODUCTION DUTIES |
|
The start of production duties was hastened by a design revue using FJVPS. Rework and frequency of trial productions of actual equipment were decreased. |
|
|
|
|
|
PRODUCT INFORMATION DATA SHARING |
|
Product information data sharing with the FJVPS server. Work efficiency, consistency and maintainability are improved. |
|
|
|
|
|
- 10% MAN-HOURS REQUIRED FOR THE ILLUSTRATIONS OF HARNESSES AND CABLES |
|
Man-hours required for document preparation were cut in half. Assembly procedure sheets, parts lists, service manuals, instruction manuals, etc. Man-hours required for the illustrations of harnesses and cables has been reduced by 10%. |
|
|
|
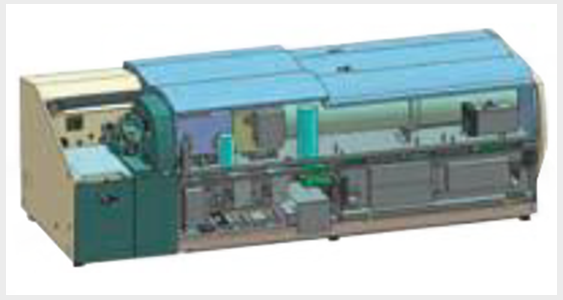 |
|
Prior study/review, decision of wiring and piping routes |
|
|
|
|
|
|
|
|
|
|
|
AMADA (Metalworking machinery and devices) |
|
|
|
|
- 50% PRODUCT DEVELOPMENT PERIOD |
|
Reduction of indirect operations, logistic cost, and improvement of maintenance serviceability have been achieved in addition to a 50% reduction of the product development period. |
|
|
|
|
|
|
- 40% DEVELOPMENT MAN-HOUR AND TIME RELATED TO WIRING AND PIPING |
|
A study/review for grouping and routing of wiring, hoses, etc. by utilizing FJVPS is executed from the planning stage. The development man-hour and time related to wiring and piping were reduced by 40%. |
|
|
|
|
|
|
|
11 MONTHS FROM DEVELOPMENT TO RELEASE ON THE MARKET IN 2 YEARS |
|
Promoting front loading, and aiming at reduction of development period & cost reduction. It was possible to shorten the period from development to release on the market to 11 months, which had conventionally required about 2 years. |
|
|
|
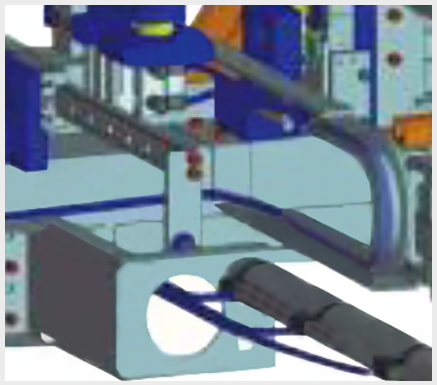 |
|
Prior study/review, decision of wiring and piping routes |
|
|
|
|
|
|
|
|
|
19% REDUCTION IN LOGISTIC EXPENSE AND A 30% REDUCTION IN THE LOGISTIC DELIVERY PERIOD |
|
FJVPS has also been utilized for the study/review on optimization of efficient loading methods on trucks as well as containers for overseas transportation. The success of such efforts has brought about a 19% reduction in logistic expense and a 30% reduction in the logistic delivery period. |
|
|
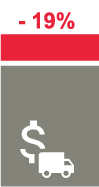 |
|
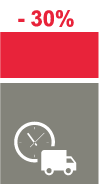 |
|
|
|
|
|
|
|
Jacto (Automatic transmssion for automobiles) |
|
|
• Challenges in reducing lead time before starting mass production. Jatco has undertaken formulation of the environment for utilizing 3D data where the functions of products, component characteristics and names, relationship with preceding & post processes about components to be assembled in charge, and precautions for safety can be learnt virtually.
• Work proficiency before formulation of a mass-production line is realized using the animation function of FJVPS. |
|
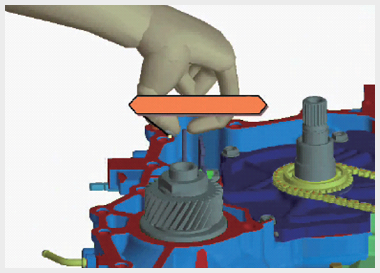 |
|
Animation for proficiency
in work at vital points |
|
|
|
|
|
|
|
|
|
|
ANIMATION FOR WORK PROFICIENCY |
|
The staff in charge of the production site can routinely make full use of DMU, and feedback knowledge of the site into the animation for work proficiency by themselves. |
|
|
|
|
|
- 40% MAN-HOURS ON THE STUDENT SIDE AFTER PROFICIENCY |
|
The variability of the teacher side was also reduced on a global scale on certain projects, and as a result, the man-hours on the student side after proficiency was also reduced by nearly 40%. |
|
|
|
|
|
|
FJVPS Capabilities / Features
FJVPS provides:
MGF
- Assembly process design
- Man Hour Calculation
- Create Assembly Procedure Animation & Manufacturing Documents
- Create BOP (Bill of design)
MDU:
- Virtual Design Review and Harness simulation
- Tool model verification and Human model simulation
- Checking Tool and Checking Operation
- Confirmation of harness movement
- Front loading development process
- Digital mockup through verification of 3D models
- Verification at early stage of designing – digital mockup
FJVPS Modules
FJVPS Standard
FJVPS Assembly Animation
FJVPS Document Interface
FJVPS Assembly Instruction Viewer
FJVPS Viewer (Free)
|
FJVPS Standard
|
FJVPS Harness
|
FJVPS Assembly Animation
|
FJVPS Document Interface
|
FJVPS Viewer
|
FJVPS Assembly Instruction Viewer
|
Display 3D-model shape |
yes |
- |
yes |
- |
yes |
yes |
Show MFG flow, MFG animation playback |
yes |
- |
yes |
- |
yes |
yes |
Measurement, Cross section |
yes |
- |
yes |
- |
yes |
- |
Create / review harness |
- |
yes |
- |
- |
- |
- |
Add annotations |
yes |
- |
yes |
- |
- |
- |
Edit assembling flow |
yes |
- |
yes |
- |
- |
- |
Assembly/disassembly animation creation |
yes |
- |
yes |
- |
- |
- |
Detecting collisions in animation |
yes |
- |
yes |
- |
- |
- |
Output flow data, Output snap shots |
yes |
- |
- |
yes* |
- |
- |
Interference/clearance check |
yes |
- |
- |
- |
- |
- |
Mechanism setting |
yes |
- |
- |
- |
- |
- |
Human, Tools |
yes |
- |
|
- |
- |
- |
Design review |
yes |
- |
- |
- |
- |
- |
Engineering change |
yes |
- |
- |
- |
- |
- |
Man-hour estimation |
yes |
- |
- |
- |
- |
- |
Assemblability evaluation |
yes |
- |
- |
- |
- |
- |
Process split, Resource assignment |
yes |
- |
- |
- |
- |
- |
Touch panel operations |
yes |
- |
yes |
- |
yes |
yes |
*Outputting flow info and snapshots made by FJVPS Assembly Animation for making various documents FJVPS Standard, MFG, DMU: Floating license
FJVPS Assembly Animation, Document Interface : Stand alone license
FJVPS Viewer: license free
FJVPS DMU is necessary to run FJVPS MFG and Harness.
FJVPS Product Requirements
Use this information to ensure you are always work with Digital Manufacturing FJVPS supported and optimized system for hardware and operating system software.
Recommended specifications |
|
|
|
|
Microsoft Windows 11 Enterprise, Pro
|
|
Microsoft Windows 10 Enterprise, Pro
|
|
|
|
|
|
|
|
|
|
|
|
2GB and above (4 GB and above is recommended)
|
|
|
|
|
|
|
|
|
|
memory 128MB and above
|
supporting OpenGL accelerator
|
|
|
|
|
|
|
|
|
|
FJICAD/SX, FJICAD/MX, NX, NX I-deas,PTC Creo Parametric (former Pro/E), PTC Creo Elements/Direct, SolidWorks, Solid Edge, CATIA V5*, Autodesk Inventor,Parasolid*, STL, VRML 2.0
|
|
|
|
|
* All Interfaces except Parasolid, JT and CATIA V5 are offered free.
Digital Manufacturing FJVPS_Brochure